Ensuring the continuity of quality testing for health products is vital to efficient medicines regulation
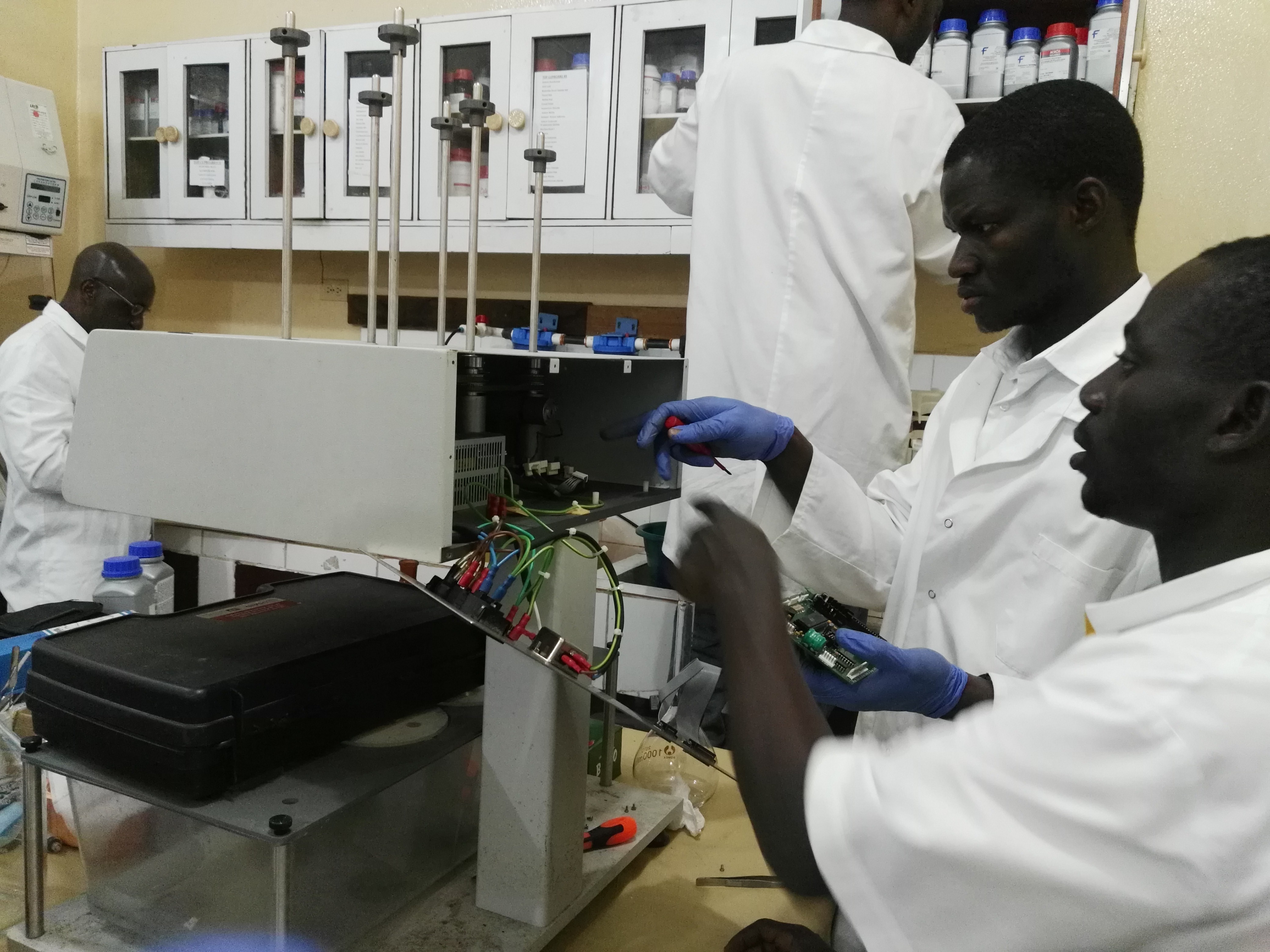
PQM program consultant, Modou Diouf (wearing blue gloves), trains Laboratory Assistant, Beware Howe, in preventive maintenance for a dissolution tester at the national quality control laboratory in Monrovia, Liberia.
Keeping medicines quality testing equipment in good working order helps ensure that national quality control laboratories (NQCLs) can continuously test the quality of health products, and thus provide timely information to medicines regulatory authorities for decisions on authorizing new medicines and on taking actions to ensure the safety of medicines already in the supply chain. While repair and maintenance are usually entrusted to the same laboratory technicians who conduct testing, the Liberia Medicines and Health Products Regulatory Authority (LMHRA) is extending training to a wider range of its NQCL staff members to better safeguard the functionality of essential machinery.
“Managers of quality control laboratories can tap into the potential of different personnel who may be interested in equipment maintenance and repair,” recommends Alexander George, Manager of the NQCL in Monrovia, Liberia. He uses the example of Beware Howe, a laboratory assistant who is responsible for cleaning glassware and work stations. Howe’s interest in equipment upkeep and the aptitude he has demonstrated are increasing assets in a laboratory where time demands on technical team members can sometimes delay needed maintenance.
Beware Howe’s curiosity was particularly clear during a 2015 site visit by the Promoting the Quality of Medicines (PQM) program, which is funded by the U.S. Agency for International Development (USAID) and implemented by the U.S. Pharmacopeial Convention (USP). PQM consultants responded by providing him with on-the-job training in basic maintenance. When subsequently given the chance to replace a faulty part in the laboratory’s water purification system, he succeeded with minimal supervision.
Under the continued guidance of the PQM program and with support from NQCL management, Howe has expanded his ability to maintain other devices. Notably, he participated in a PQM-led advanced training for NQCL technical staff on preventive maintenance and installation of laboratory equipment in early 2018. “Good on-the-job training is enough to meet any repair and maintenance needs associated with laboratory equipment such as high performance liquid chromatography units, ultraviolet-visible spectrophotometers, dissolution testers, disintegration testers, pH meters, and analytical balances,” says Alexander George.
LMHRA’s readiness to broaden its approach to capacity-building for maintenance of laboratory equipment is not only strengthening efficiency at NQCL, but also improving cost-effectiveness. For example, the laboratory has realized significant cost savings by routinely maintaining its water purification system so that micro-filters (costing 300 USD) only need replacement twice a year instead of monthly.
The PQM program’s partnership with LMHRA has shown that building an NQCL’s capacity for equipment maintenance improves operational efficiency by lowering the cost of operating testing devices and reducing the frequency of repairs. Expanding the types of staff members who receive training better ensures that such capacity is available and used on a continuous basis.
The Promoting the Quality of Medicines (PQM) program has been providing technical assistance to build the capacity of Liberia’s National Quality Control Laboratory since 2009.